Verdens første kjøretøy fremstilt av fossilfritt stål. Dette var den store nyheten da Volvo-konsernet rullet ut en dumper på et pressearrangement i Gøteborg i oktober i fjor.
Dumperen, er en kraftig lastemaskin på hjul som skal brukes til å frakte tunge gjenstander i gruver og steinbrudd.
Dumperen er den første prototypen fra det svenske stålkonsernet SSABs ambisiøse prosjekt for å bytte fra en konvensjonell, svært klimaskadelig produksjon av stål, til en mye grønnere prosess, nemlig fossilfritt stål i følge konsernet.
SSAB forventer å kunne innvie det første storskalaanlegget for industriell produksjon av fossilfritt stål i 2026. I årene etter vil konsernet ta konvensjonelle anlegg ut av drift, da nye renere anlegg kan tas i bruk.
Også andre stålselskaper i Norden er inne i en grønn omstilling. Metoden er å gå over til en mer klimavennlig produksjonsmetode og/eller øke gjenvinningen av jern- og stålskrap til stålproduksjon. Norden er dermed i front globalt i en sektor som kan utgjøre en merkbar forskjell for klodens CO2 utslipp.
Max Åhman er førsteamanuensis i studier av miljø og energisystemer ved Lunds universit i Sverige. Han forteller at det har skjedd mye med energieffektivisering i stålproduksjonen de siste tiårene, men det er ikke nok i forhold til klimamålene.
– Det trengs en annen teknologi. Løsningene er der, og det burde ikke være noe problem med tilpasningen. Den store utfordringen er å få til en storskala satsing, slik at det blir lønnsomt for selskapene og at det integreres i verdikjedene, sier Max Åhman.
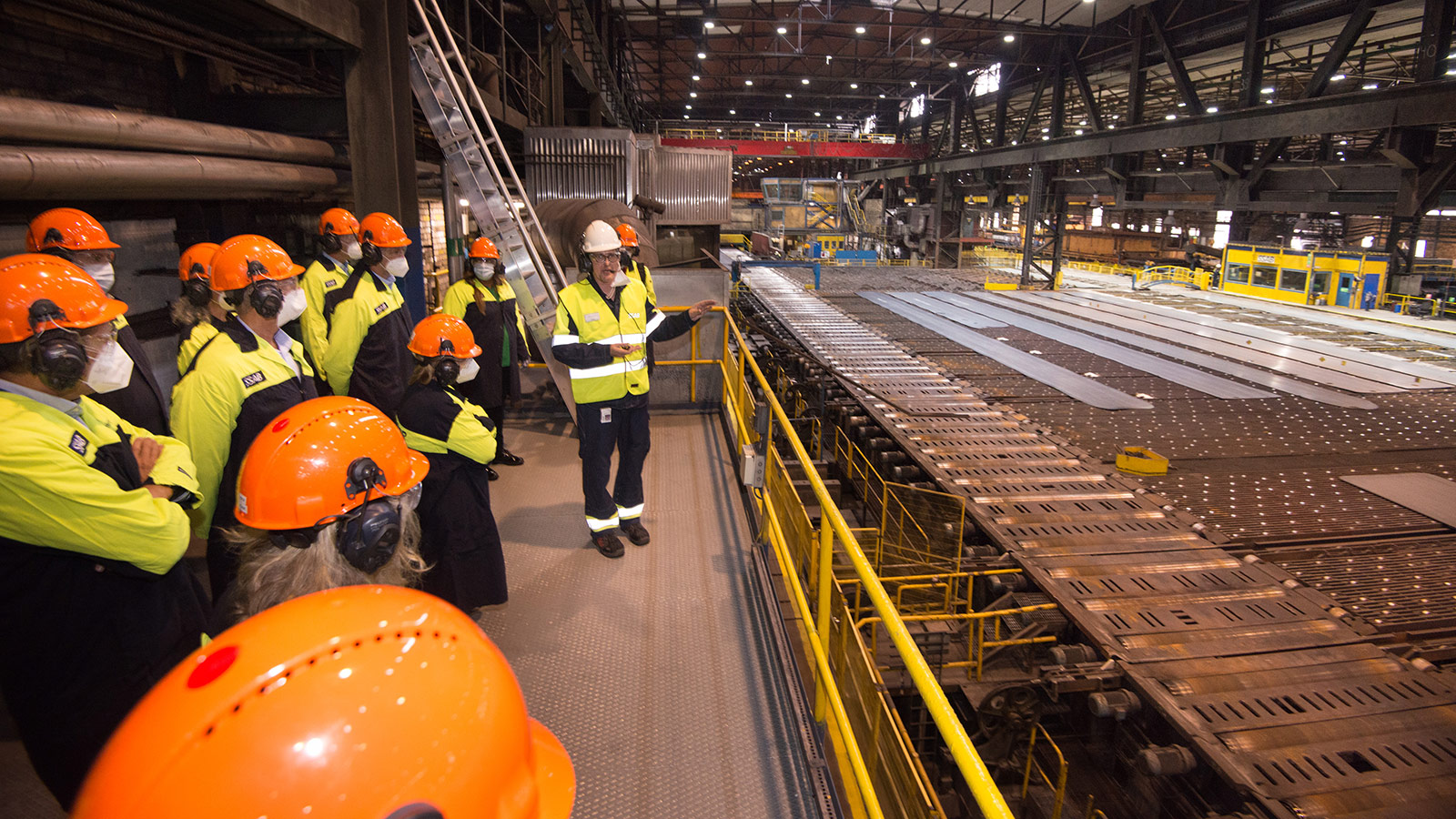

Enormt energiforbruk i prosessen
Produksjonen av stål står for fem prosent av de globale utslippene av CO2 og andre klimagasser. Dette er estimert av FNs klimapanel. Andre beregninger viser opp mot åtte prosent. Utslippene er uansett større enn fra for eksempel flytrafikken som det er mye oppmerksomhet rundt.
Stålproduksjon er en av næringene i verden som forurenser mest på grunn av det enorme energiforbruket i prosessen, i tillegg til råvarene som brukes.
Samtidig er stål et helt uunnværlig materiale fordi det brukes i konstruksjoner, transportmidler, maskiner og mye mer. Internasjonal etterspørsel har omtrent doblet seg siden årtusenskiftet og forventes å øke ytterligere fremover.
Stål er laget av jernmalm utvunnet i gruver. Jernmalmen smeltes ved en såkalt reduksjonsprosess i masovner, hvor det produseres råjern, som er et mellomprodukt på vei til stål. Metoden dukket opp i andre halvdel av 1800-tallet og er fortsatt nesten helt dominerende. Som brensel brukes koks, som har den tilleggsfunksjonen at jernmalmen under smeltingen frigjør oksygen (oksider) fra jernoksidene ved svært høy varme. Dette oksygenet, som dermed frigjøres, binder seg til karbonet under smelteprosessen, og produserer store mengder CO2.
For å utvikle råjern til stål tilsettes ulike andre metaller slik at stålet oppnår ønskede egenskaper for bygg og industri. Det ferdige stålet rulles deretter ut til plater eller lages til konstruksjonsstål eller andre såkalte stålemner. Flere av de tilsatte såkalte legeringsmetallene er også bundet til oksygen, inkludert krom. Dermed er det også et CO2-bidrag fra legeringsmetallene under oppvarmingen, påpeker Per Kalvig. Han er sjefskonsulent ved Kunnskapssenteret for mineralråstoffer og materialer under den uavhengige danske forskningsinstitusjonen The National Geological Survey (GEUS).
Per Kalvig etterlyser derfor fokus på at CO2-bidraget fra stålproduksjonen ikke bare kommer fra masovnene og deres bruk av kullkoks. I tillegg kommer betydelige bidrag fra selve gruven med jernmalm, fra transport av jernmalm fra gruven, samt fra produksjonen av legeringsmetallene som brukes.
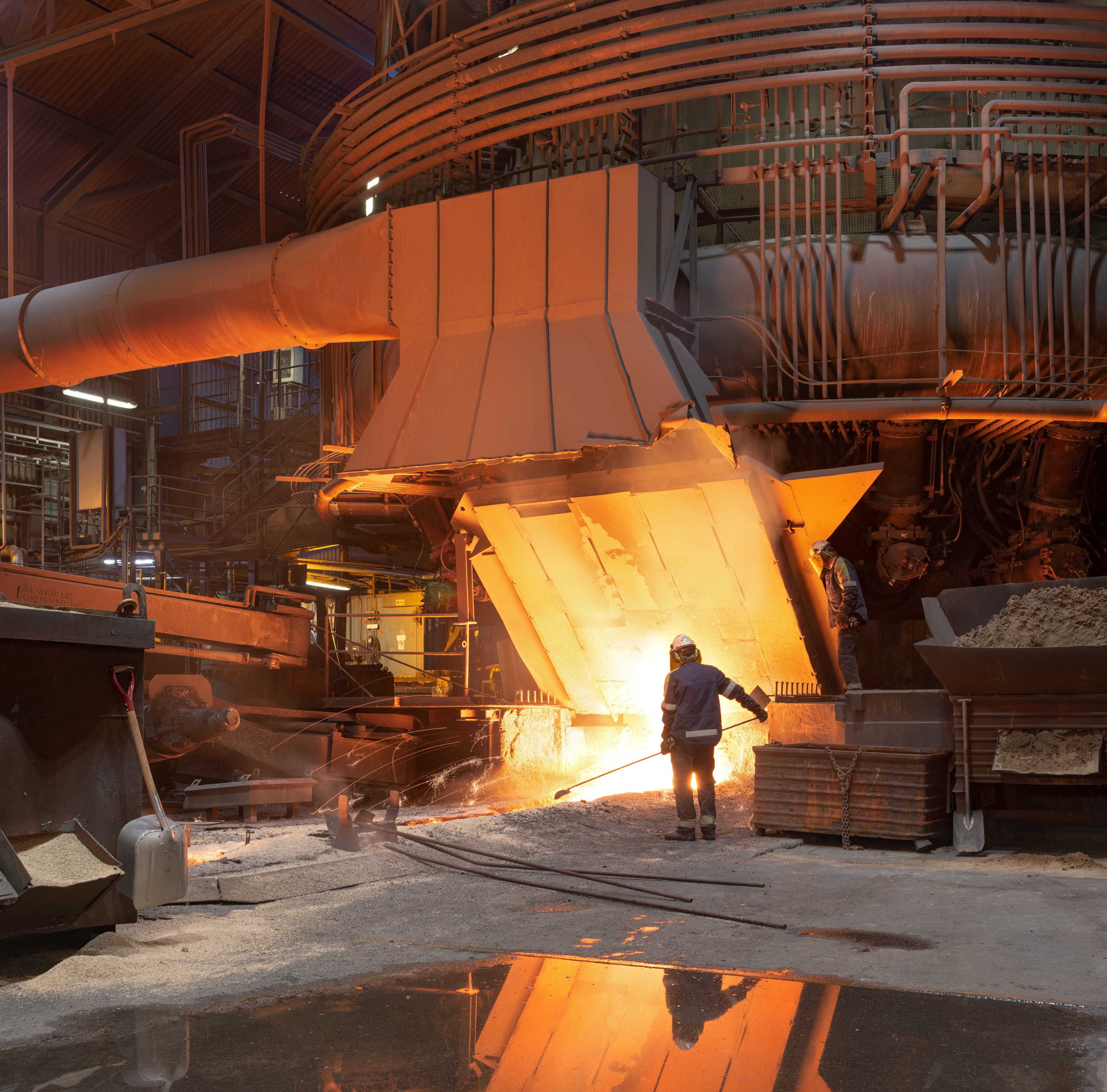
Hydrogen fra grønn elektrolyse
Nøkkelen til å gjøre stålproduksjon mye grønnere er å erstatte koks og annet fossilt brensel med hydrogen, som utvikles på grunnlag av vann gjennom elektrolyse (= en nedbrytning ved bruk av elektrisitet). Elektrisiteten skal komme fra fossilfrie energikilder. Hydrogenet fjerner karbonet fra jernmalmen, og da blir det vann til overs. Vannet kan også resirkuleres i elektrolyseprosessen.
I overgangen til hydrogen må masovner skiftes ut med såkalte lysbueovner drevet av hydrogen fra grønn strøm, dette som en del av det som kalles en direkte reduksjonsprosess.
Så langt har CO2-fangst vært sett på som en måte å redusere den negative klimapåvirkningen av stålproduksjon på, men det har vært en elektrifisering av en rekke samfunnsfunksjoner i de senere årene, blant annet av vind- og solenergi. Prisen på disse energikildene er synkende, noe som gjør de attraktive for en mer klimavennlig stålproduksjon, sier Max Åhman.
I både Sverige og Norge er det også rikelig med vannkraft. Sverige har også atomkraft, som inngår i beregningen som en fossilfri energikilde.
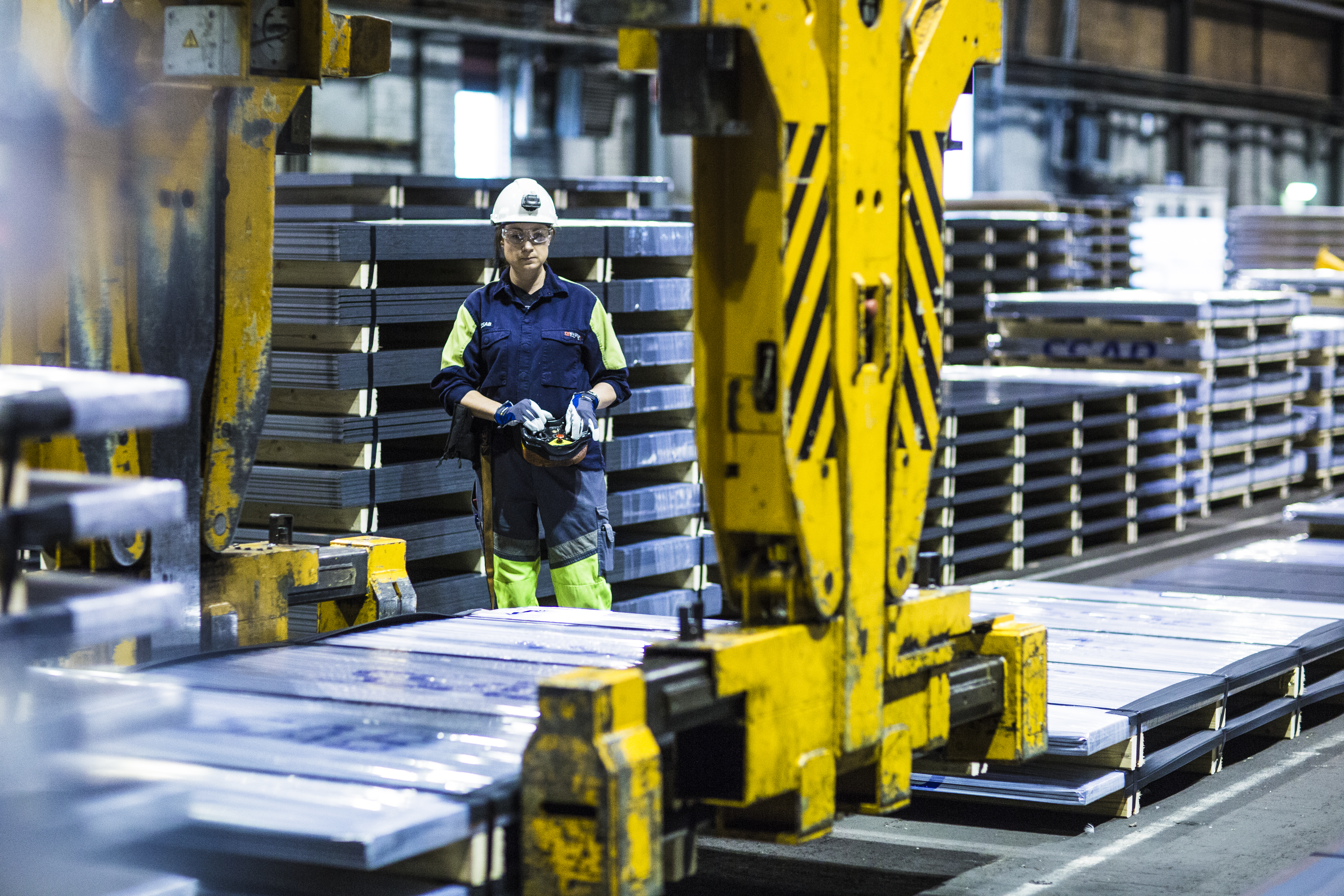
Ikke redusering, men eliminering av CO2
Thomas Hörnfeldt fra SSAB opplyser at målet er fullskala fossilfritt stål.
– Vi snakker ikke om å redusere CO2-utslippene. Vi snakker om å eliminere CO2-utslipp. Vi bygger noe nytt fra bunnen av. Det avgjørende her er at vi gjør det sammen med partnere, slik at hele verdikjeden i produksjonen blir fossilfri, sier Hörnfeldt, som understreker at LKAB er opptatt av å bli fossilfri, og at Vattenfall bygger ut vindkraft og lover å levere fossilfri strøm eksklusivt til stålproduksjonen.
Både LKAB og Vattenfall eies av den svenske staten og gir støtte til deler av HYBRIT-prosjektet.
Thomas Hörnfeldt forteller at det er mulig å lage stål i samme kvalitet og i samme typer som før med den nye prosessen. Den store endringen er i den første fasen, nemlig produksjonen av råjern.
Han forventer at prisen på fossilfritt stål blir litt dyrere enn konvensjonelt stål. En intern eldre studie viste en økning pr enhet på 20-30 prosent.
– Men dette er stålprodukter av høyere verdi fordi de er fossilfrie, og vi forventer at prisforskjellen blir mindre – for eksempel som følge av prisingen av CO2-utslipp, sier Hörnfeldt.
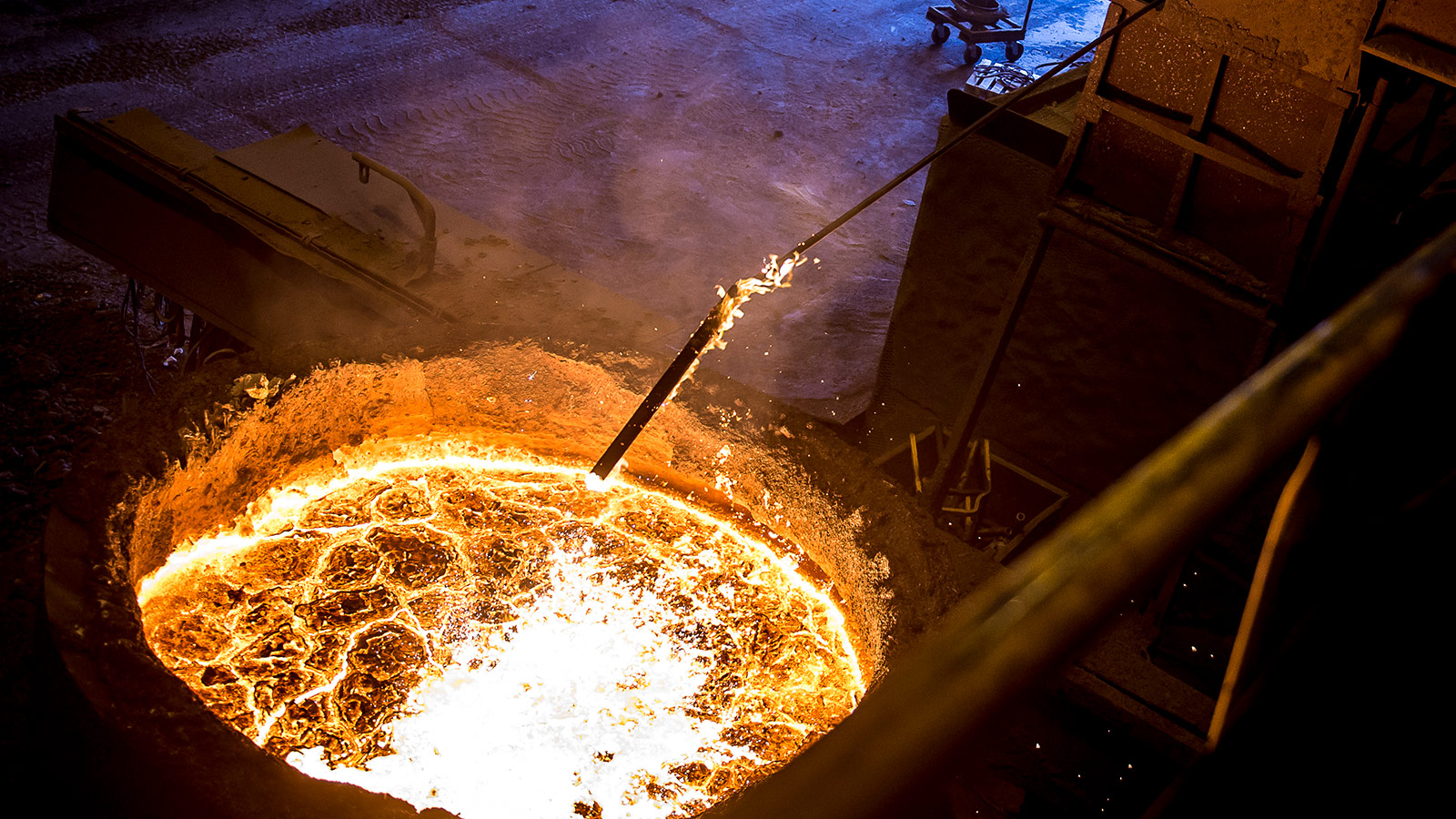
Gjenbruk av skrapstål i Mo i Rana
Det er to veier til stålprodukter. Den ene er å produsere helt nytt stål. Den andre er å resirkulere gammelt skrapstål om til nytt stål. Omtrent en tredjedel av verdens stålproduksjon skjer på grunnlag av skrap.
Stålprodusenten CELSA Nordic med base i Mo i Rana er Nordens ledende produsent av stål ved gjenbruk av jern og skrapstål. De primære stålproduktene er armeringsstål for bygninger og fysisk infrastruktur.
– Vårt CO-avtrykk ved bruk av skrap er allerede en niendedel av det som slippes ut i konvensjonell stålproduksjon, sier CELSA Nordics direktør, Ignacio Pérez. Han er spansk, og CELSA Nordic er den spanske CELSA-gruppens forretningsenhet i fire nordiske land, nemlig Norge, Sverige, Finland og Danmark.
Pérez opplyser at stål basert på skrap har samme kvalitet, bruk og pris som annen stål.
CELSA Nordic har også et mål om å kunne produsere stål som er helt fossilfritt.
For øyeblikket omsmeltes skrap til flytende stål med strøm fra vannkraft. Men neste steg i prosessen, som er å produsere armeringsstål, skjer i en ovn med overskuddsgass fra et nærliggende selskap som varmekilde.
– Vi jobber med å utvikle en ovn som drives av grønt hydrogen, som produseres med vannkraftelektrisitet. Det er selvfølgelig en teknologi vi må utvikle. Vi ønsker å være helt CO2-nøytrale, sier Ignacio Pérez.
Tilgang til skrap kan være en utfordring for å møte det økende behovet for «grønt» stål, men CELSA Nordic-direktøren håper på politisk vilje i Europa for innsamling av mest mulig skrap.
– Den grønne omstillingen i sektoren bør stimuleres. Vi er en del av en sirkulær verdikjede, og det største potensialet i forhold til klimapåvirkning ligger tidlig i verdikjeden. Det vil si i selve stålproduksjonen, sier Ignacio Pérez.
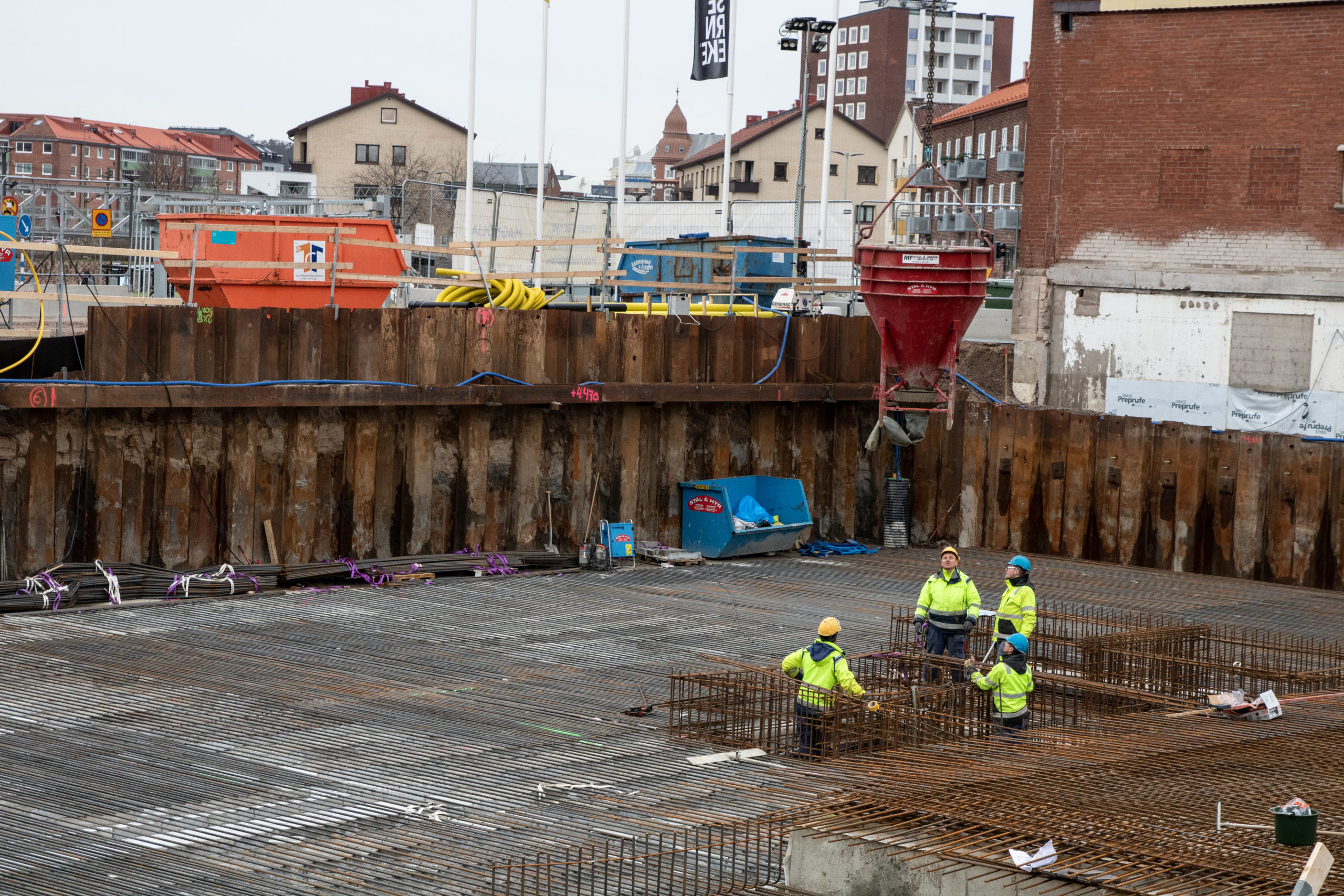
Kjøpere og investorer presser på
Både SSAB og CELSA Nordic kan merke en økt interesse blant kjøpere av stålprodukter for mer bærekraftige produkter. Mye har skjedd de siste årene.
– Generelt har kunder begynt å be om miljøvaredeklarasjon og de vil vite mer om skrapstål. Vi kan se at produktene våre blir mer verdsatt på markedet nå, sier Ignacio Pérez fra CELSA Nordic.
– Mange ønsker mer bærekraftige produkter, og vi kan tilby kundene å bli en del av den fossilfrie verdikjeden, sier Thomas Hörnfeldt hos SSAB.
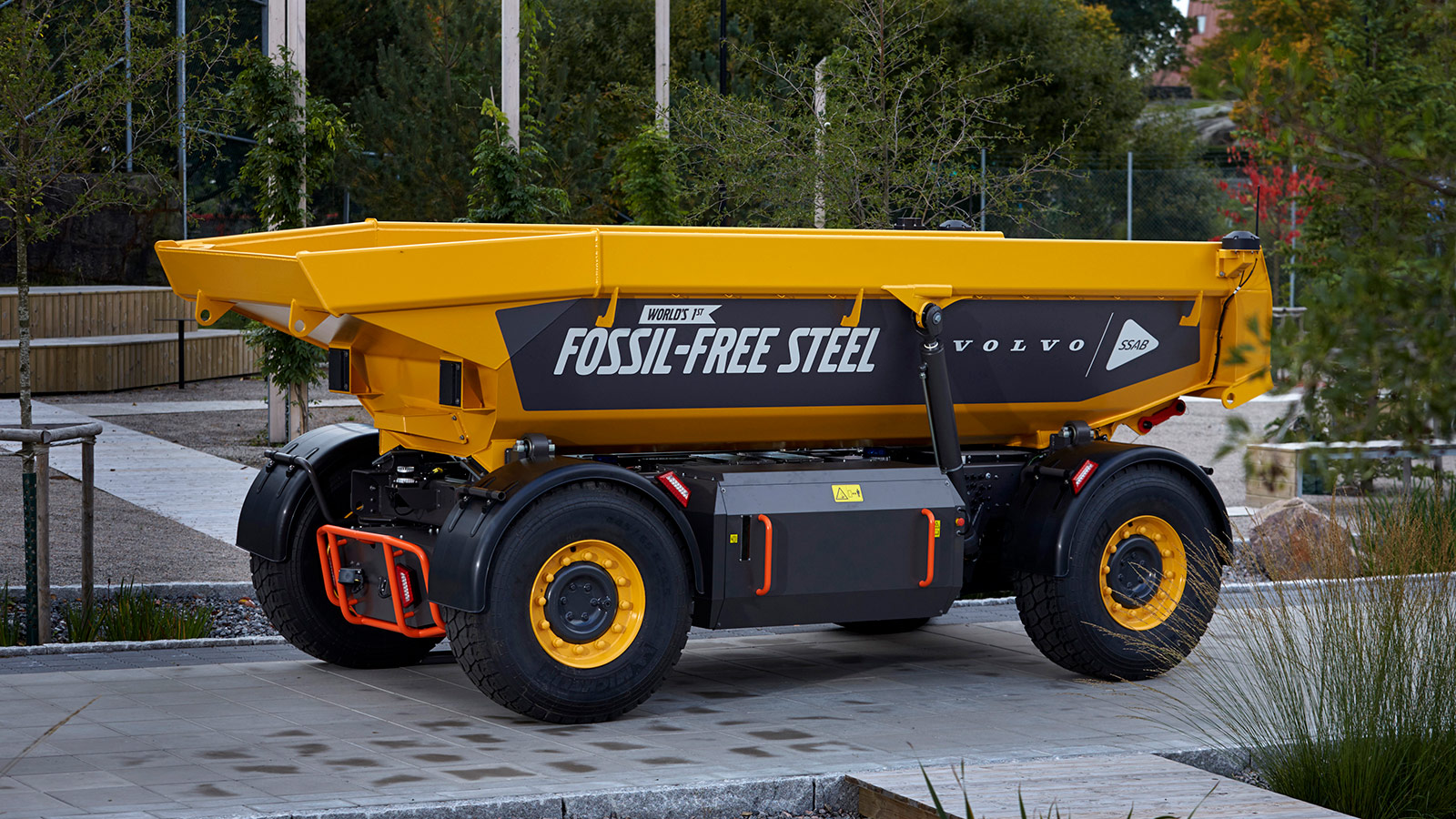
Volvo-konsernet, som har avtale om leveranser fra SSAB, beskriver det som avgjørende i forhold til potensielle kjøpere av personbiler, busser og lastebiler at fossilfritt stål skal inngå i kjøretøyene. 35 prosent av CO2-utslippene fra materialene i Volvos bensin- og dieselbiler kommer i dag fra stål. Andelen er 20 prosent i elbiler.
– Vi ønsker å ta tak i alle kilder til fossile utslipp. Volvo har som mål å kjøpe og bruke fossilfritt stål i større grad i produksjonen ettersom det produseres større mengder fossilfritt stål. Vi har et bærekraftsmål om at alt som forlater fabrikkene våre skal være helt fossilfritt innen 2040, sier Claes Eliasson, Senior Vice President for Group Communication i Volvo Group.
De nordiske stålprodusentene opplyser at ikke bare kjøpere, men også investorer kan føle en økt bevissthet rundt den grønne profilen.
Max Åhman fra universitetet i Lund oppfordrer investorer til å tenke langsiktig.
– Det tar tid å transformere stålsektoren. Derfor må investorene snart bestemme seg for hvordan de vil at sektoren skal se ut i 2050, sier Åhman.
Hans appell må ses i lys av en vurdering fra Det internasjonale energibyrået om at utslippene fra stålproduksjonen må halveres innen 2050, dersom globale klima- og energimål skal nås.